This new technology could kill the business case for hydrogen in green steel production
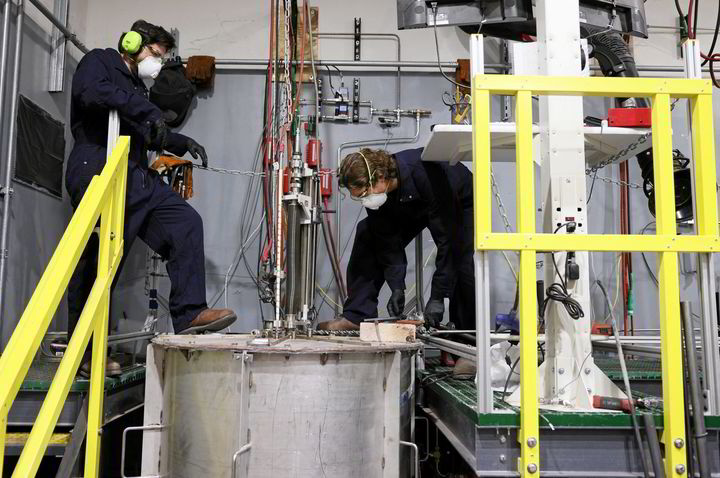
It has been a long-held view that the only possible way to decarbonise steel production is to use green hydrogen to extract iron from ore, and then use electric arc furnaces to turn the iron into steel.
But a long-gestating technology being developed by a well-funded start-up promises to not just compete with green hydrogen, but potentially destroy the business case for H2 in steel production altogether.
Massachusetts-based Boston Metal has invented a technology it calls molten oxide electrolysis (MOE) that blasts a liquid electrolyte containing iron ore pieces with large amounts of clean electricity, heating it to 1,600°C (the melting point of iron) via an electrode able to withstand such high temperatures.
At this temperature, the iron oxide in the ore splits into pure molten iron and oxygen; impurities such as silica and magnesium rise to the top of the furnace, and the liquid electrolyte remains in situ to continue the process.
Another advantage of the technology is that while hydrogen-fired direct-iron reduction (DRI) (see panel below) requires scarce high-grade iron ore — causing Swedish developer H2 Green Steel to import ore from Canada and Brazil — MOE works with low-grade iron ore, a cheaper resource.
Boston Metal already operates a pilot plant at its headquarters in Woburn, Massachusetts, and is this week due to open a commercial-scale factory in Brazil producing low-carbon iron alloys, which the company believes can bring in $400m of revenue by 2026 — the year it hopes to start making green steel commercially, according to Forbes magazine.
Article continues below the advert
It is a good job that Boston Metal has been well-funded — it has been working on MOE technology since its formation in 2013, and the company’s potential is so large that it has continued to attract high-profile investors.
Breakthrough Energy Ventures — the tech venture capital firm funded by billionaires such as Bill Gates, Jeff Bezos and Richard Branson — was one of Boston Metals’ early financial backers, and continues to support the company, contributing an undisclosed amount last September to a Series C funding round that raised a staggering $262m.
Venture-capital database Pitchbook recently valued the company at $860m, according to Forbes.
Another Series C investor was steel giant ArcelorMittal, which is set to receive €2.89bn from European governments to build DRI facilities, even though its Europe boss recently admitted that green hydrogen was too expensive to use in its EU steel mills.
Estimates suggest green hydrogen-based steel will be 20-40% more expensive than grey steel made with coal-fired blast furnaces and basic oxygen furnaces.
But Boston Metal CEO Tadeu Carneiro told Forbes that its technology would enable the production of green steel to reach cost parity with the highly polluting variety once MOE plants produce between one and two million tonnes a year, with electricity prices of about $30/MWh — a figure already being reached by solar power in the sunniest parts of the world.
“We want to make a better metal at a lower price without a subsidy,” he said. “A premium means you failed. Your technology is not market-ready.”
Nevertheless, plenty of offtakers have been willing to pay a premium for hydrogen-derived green steel. For example, H2 Green Steel has already signed binding offtake agreements with Mercedes-Benz, Porsche, truck maker Scania, US conglomerate Cargill, German auto technology firm ZF, German auto parts supplier Kirchhoff Automotiv, Italian steel maker Marcegaglia, UK-based SPM and Germany’s Bilstein Group.
Replacing grey steel made using coal with the more expensive green variety will cost about €300 ($326) per car, according to estimates — an increase that can be fairly easily absorbed by customers already paying five figures for new vehicles.
Boston Metals’ MOE technology can also be used to produce low-carbon metals other than iron and steel. In November, the US government awarded funding to allow Boston Metal to build a new facility in West Virginia to manufacture ultra-pure chromium. The exact amount of funding was not revealed, but the project was one of seven to share a cash pot of $275m.
Green steel producers are planning to use green hydrogen to decarbonise their steel mills, which together account for 7-8% of all global carbon emissions.
Traditionally, iron has been extracted from iron-oxide ore by burning carbon-rich coking coal in a blast furnace, where the fossil fuel produces high-temperature heat while simultaneously removing oxygen from the ore by converting it to carbon dioxide.
This highly polluting method can be replaced with green hydrogen in a direct-reduced iron (DRI) facility, where the H2 reacts with the oxygen to produce steam (H2O) rather than carbon dioxide.
In fact, hydrogen-based DRI is currently the only proven pathway of decarbonising steel production, when paired with an electric arc furnace powered by renewable energy.
Policymakers want producers to eliminate emissions from the sector by using green-hydrogen DRI that is then turned into green steel using renewables-powered electric arc furnaces, but with green H2 costing in excess of €5/kg in Europe, it would result in significantly more expensive steel that will require offtakers to pay a premium.
Your point of view caught my eye and was very interesting. Thanks. I have a question for you.