Hydrogen-derived steel set to be used in wind farms for the first time, but how green will it be?
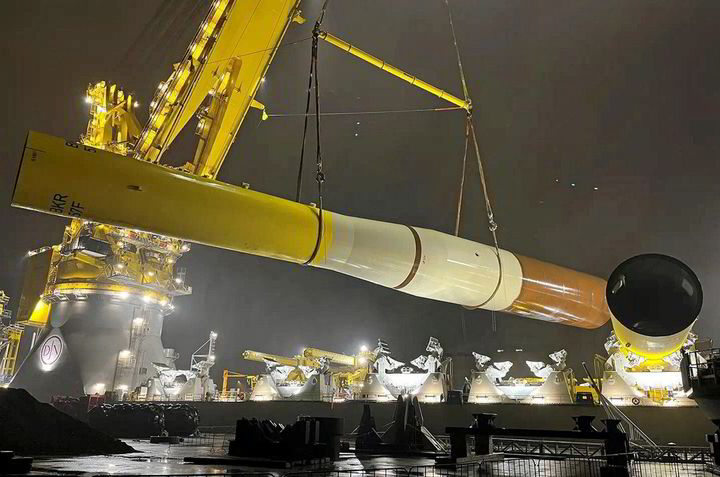
Denmark’s Orsted yesterday (Wednesday) signed a preliminary agreement with German steel plate producer Dillinger which could see the first wind farm components made with H2-derived steel manufactured for the Danish company by 2028.
While not a commitment to offtake any volumes, the memorandum of understanding (MoU) gives the Danish wind developer right of first refusal on Dillinger’s low-emissions steel made with hydrogen, once its green steel plant is up and running.
It puts Orsted in position to be one of the first to operate wind farms built with steel derived from H2, although it is far from clear whether it would be the very first, or even the cleanest.
In fact, the “lower-emissions” steel mooted in yesterday’s agreement will be made with some fossil fuels — with the direct-reduced iron (DRI) used for Dillinger’s green steelmaking (see panel below) made with 50% methane and 50% H2 to begin with.
The MoU between the pair envisages Orsted offtaking “lower emission” steel plates (a processed steel product) made at Dillinger’s Dillingen steel mill in Germany from 2027-2028, which will be used to manufacture monopile foundations for offshore wind turbines across Orsted’s vast development pipeline.
Dillinger is planning a direct-reduced iron plant at Dillingen, as well as two electric arc furnaces at its Völklingen steel plant 400km away, with the aim of producing a total of 3.5 million tonnes of “green steel” in 2027-2028.
Article continues below the advert
Green steel producers are planning to use green hydrogen to decarbonise their steel mills, which together account for 7-8% of all global carbon emissions.
Traditionally, iron has been extracted from iron-oxide ore by burning carbon-rich coking coal in a blast furnace, where the fossil fuel produces high-temperature heat while simultaneously removing oxygen from the ore by converting it to carbon dioxide.
This highly polluting method can be replaced with green hydrogen in a direct-reduced iron (DRI) facility, where the H2 reacts with the oxygen to produce steam (H2O) rather than carbon dioxide.
In fact, hydrogen-based DRI is currently the only proven pathway of decarbonising steel production, when paired with an electric arc furnace powered by renewable energy.
Policymakers want producers to eliminate emissions from the sector by using green-hydrogen DRI that is then turned into green steel using renewables-powered electric arc furnaces, but with green H2 costing in excess of €5/kg in Europe, it would result in significantly more expensive steel that will require offtakers to pay a premium.
Neither company has yet revealed how much lower-emissions steel Orsted intends to contract. However, the Danish firm says it has placed a large order for conventional steel, which it believes will underpin some of the €3.5bn ($3.83bn) investment necessary to bring the DRI plant and electric arc furnaces to fruition.
“Long-term offtake agreements [of conventional steel] like this one are key to decarbonising hard-to-abate materials such as steel because it takes clear demand signals to drive investments in the technologies needed to decarbonise production,” said Virginie Van de Cotte, chief procurement officer at Orsted.
“With this MoU, we’re pleased to help support Dillinger’s development of lower-emission steel facilities in Europe. This is an agreement which will also enable Orsted to further diversify its supply chain, secure capacity, and deliver on expected future customer demand.”
In December 2023, Germany’s federal government recently granted €2.6bn in decarbonisation subsidies to steel manufacturers in the Saarland region, where Dillingen and Völklingen are located.
However, it is not clear how much of the funding, which is now pending approval from the EU, would be allocated to the two plants, nor whether it would be sufficient for Dillinger’s parent company Stahl-Holding-Saar to sanction a final investment decision (FID).
Process emissions
The low carbon steel produced at Dillingen would reduce the “process emissions” from producing the monopiles by 55-60% compared to conventional steel, Orsted said.
Steel production can approach zero emissions, if green hydrogen is used in DRI production and if the steel-making process is powered by renewable energy.
However, the steel at Dilligen’s mill would be made with DRI produced from a mixture of both green hydrogen and fossil gas, with only 50% H2 used at first.
The German company is targeting an 80% hydrogen to 20% methane ratio by 2030, although this will depend on the “market availability” of green hydrogen, a spokesperson for Dillinger told Hydrogen Insight today.
“Natural gas will be used in the DRI plant as a bridge until sufficient hydrogen is available,” he said, noting that the plant will only use H2 made with renewables.
Orsted pointed out that the company struck the deal with Dillinger on the back of the EU’s recently-passed Net Zero Industry Act, which forces host governments to consider non-price criteria when auctioning renewable energy contracts.
“Thus, the agreement with Dillinger not only helps accelerate the decarbonisation of the steel industry; it also provides Orsted with the optionality to deliver on expected decarbonisation criteria in coming auctions when they materialise,” the company said in a press release.
However, although Orsted is certainly an early mover on using H2-derived steel in its wind farms, it may not be the first to put them into operation.
Last year Swedish energy firm Vattenfall, which is an investor in Sweden-based Hybrit green steel programme, which makes 100% green hydrogen-based DRI, announced that it could start buying volumes of near-zero emissions steel (made using Hybrit DRI) from Hybrit co-investor and steel producer SSAB as early as 2024.
Vattenfall has not specified exactly how it would use the green steel, should the deal come to fruition, saying only that it could be used across a variety of applications, including power lines, hydroelectric dams, grid stations, anchoring for onshore wind power or parts of foundations for offshore wind.
Otherwise, hydrogen-based green steel has so far not played much of a part in supply chain decarbonisation for wind developers, despite the fact that steel makes up 80-90% of a wind turbine’s material mass and 50% of its total lifecycle emissions.
Siemens Gamesa is developing a “GreenerTower” for installation at the 1GW Thor offshore wind farm in Denmark, for which it has a deal with Germany’s Salzgitter to procure low-emission steel plates.
However, the agreement does not envisage a supply from Salzgitter’s green hydrogen-based steel programme, instead using materials produced using scrap metal and renewable power.
Danish turbine manufacturer Vestas, along with Orsted, last year agreed to procure low-carbon steel towers and blades made from recycled materials, while Vestas has separately committed to buy low-emissions steel from steelmaker ArcelorMittal, made with scrap metal smelted in an electric arc furnace.
Nordex, meanwhile, has pledged to make all the blades on its wind turbines recyclable, while several other OEMs have made only vague commitments, or none at all.
Spain’s Iberdrola has committed to use 10% of “near zero” steel across all its operations (which includes wind developments), 50% low emissions steel by 2030 and 100% low emissions steel by 2050 — a pledge made as part of the SteelZero programme, of which Orsted, Vattenfall and Siemens Gamesa are also signatories.
Hydrogen Insight contacted Orsted for comment but the company had not responded at the time of publication.