Hydrogen Electrolyzers 101: Why They Matter for Sustainable Energy
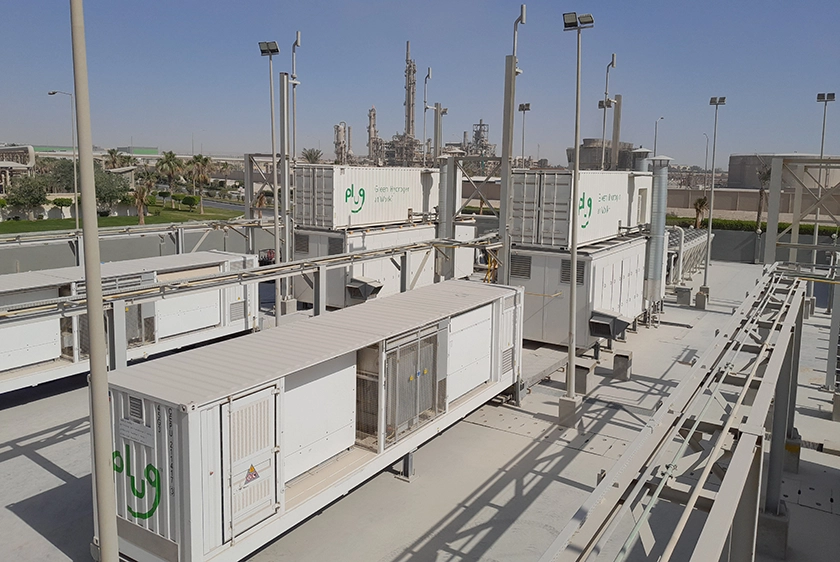
What is an electrolyzer? And what kind of role will they play in helping the world meet net-zero goals? Here is the A to Z of electrolyzers.
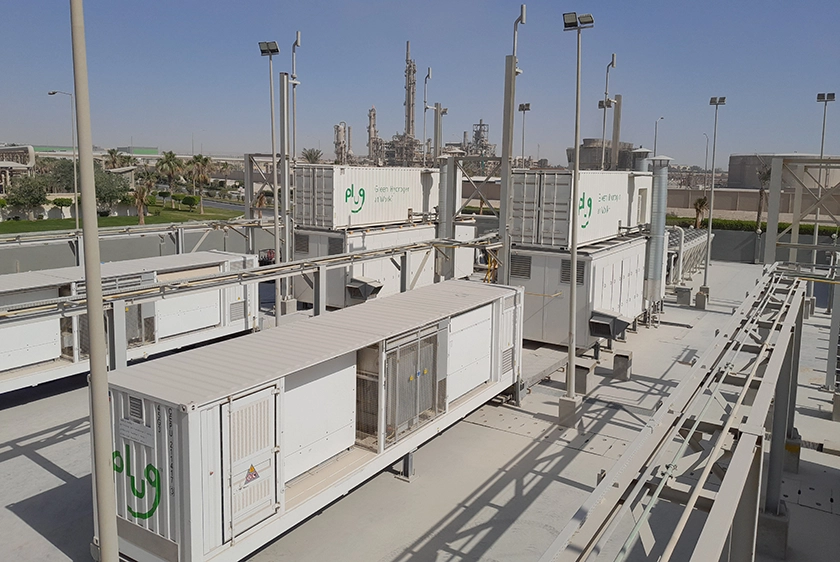
A. Introduction to Electrolyzers
If solar power is defined by solar cells and wind production propelled by wind turbines, then the equivalent for green hydrogen production is the electrolyzer.
Put another way, an electrolyzer serves as “the building block of green hydrogen,” Plug President and CEO Andy Marsh told Bloomberg in July 2022.
B. Benefits of Electrolyzers
Electrolyzers that use renewables to power their hydrogen production – like wind, solar, hydroelectric power, or certain biofuels – churn out emissions-free production of green hydrogen.
Down the value chain, green hydrogen will prove increasingly crucial for the production of green ammonia and methanol, chemical compounds crucial for the future of more sustainable agricultural practices, chemical production, and seaborne shipping.
Beyond output value, electrolyzers can also be used for longer-term energy storage, producing hydrogen that is stored in pressurized vessels for later use, with “much higher storage capacity compared to batteries (small scale),” according to the alternative energy advocacy organization American Clean Power.
C. Components of Electrolyzer Stacks
Electrolyzers essentially function like fuel cells, but in reverse.
At the most basic level, water is provided to the electrolyzer stack, which looks like a multi-decker sandwich. The three layers in PEM electrolyzers utilized by Plug – called a cathode, an anode and a special membrane painted with a catalyst to separate the water into hydrogen and oxygen, using electricity to power the reaction. The hydrogen is then captured and stored for a variety of end uses.
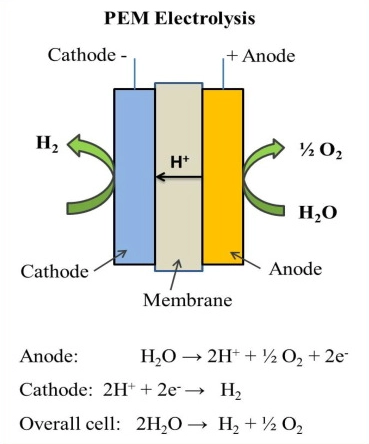
D. Different Types of Electrolyzers
There are three different water-splitting electrolyzer types: Alkaline, Solid Oxide, and Proton Exchange Membrane, the latter of which is utilized by Plug.
Alkaline electrolyzers use water and a liquid electrolyte, generally either potassium hydroxide or sodium hydroxide. They run at an internal temperature of just below 100°C. Solid oxide electrolyzers, sometimes also known as solid oxide electrolysis cells (SOECs), make use of a solid oxide ceramic electrolyte in producing hydrogen. Those run at internal temperatures of 500oC to 850oC.
And PEM electrolyzers utilize a proton exchange membrane functioning as a solid polymer electrolyte. When electricity runs through the stack during the water electrolysis process, the water splits into hydrogen and oxygen. Hydrogen then passes through the membrane and ejects on the cathode side. PEM electrolyzers run at ideal temperatures of 60oC to 80oC.
E. Electrolysis Process
The water electrolysis process utilized within Plug’s PEM electrolyzers is an electrochemical process that splits water into hydrogen and oxygen gases. At its simplest, the stack consists of a multi-decker sandwich of anodes and cathodes separated by proton exchange membranes coated in catalyst.
Here’s a simple explanation of how a PEM electrolyzer works:
- Water supply: the electrolyzer requires a source of water, which can be provided through a water inlet
- Electrolysis process: when the power supply is turned on, an electric current flows through the electrolyte and causes a reaction at the electrodes:
- Anode (oxidation): at the anode, water molecules lose electrons and are oxidized. This reaction produces oxygen gas (O2), and positively charged hydrogen ions (H+) and releases electrons.
- Cathode (reduction): at the cathode, the hydrogen ions and electrons combine to form hydrogen gas (H2).
- Membrane function: the proton exchange membrane, coated in catalyst, allows only the positively charged hydrogen ions (H+) to pass through while blocking the electrons. This creates a separation of charges and generates a flow of protons from the anode to the cathode through the membrane.
- Gas Separation: as the electrolysis process continues, the hydrogen gas produced at the cathode side and the oxygen gas released at the anode side are collected separately.
- Gas Output: the collected hydrogen and oxygen gases can be used for various applications, such as fuel cells, industrial processes or energy storage.
Those aiming to produce green hydrogen, for which Plug is working to be a global-leading producer, make use of renewable energy sources like wind, solar, biomass, or hydro-electric power.
F. Factors Affecting Electrolysis Efficiency
While many factors determine the efficiency of the electrolysis process, temperature serves as a significant driving force.
This makes SOECs the most efficient electrolyzer fuel cell stack array according to most experts, but the extremely high temperature it requires to function also makes it the least versatile for that same reason. That’s because it takes more energy and time to power up to temperatures needed to carry out the electrolysis process. In other words, efficiency always comes within its own context and sits in the eye of the beholder.
Other key factors affecting electrolysis efficiency include electrolyte quality, electrical resistance of the electrolyte, the type of electrode material used, pressure applied for the current within the electrolyzer, varying types of separator and catalyst materials, and applied electricity voltage waveform.
A study published in the Journal of Electrochemical Science and Technology concluded that “concentration of [potassium hydroxide in] the electrolyte significantly affected the electrolyser performance” and that PEM electrolyzers “offer several advantages over traditional technologies including…higher production rates and more compact design,” in pointing to other electrolyzer efficiency factors.
G. Hydrogen Storage and Transportation
Hydrogen can be both stored and transported multiple ways.
For storage, while pressurized vessels are still useful for materially significant levels of storage, for larger amounts, underground caverns or ground-based storage tankers serve as the primary means of storing hydrogen.
The U.S. Department of Energy’s National Energy Technology Laboratory has also cited the prospect of storage in metal hydrates, surface-area absorption, and legacy natural gas pipelines as prospective hydrogen storage mechanisms. The agency states, however, that all of these except for the pipeline option are “still in the early stages of research and development, and as of yet it has not been shown to be energy or cost efficient.”
And for transportation, due to lack of pipeline infrastructure, the dominant method of moving hydrogen to market today is via cryogenic long-haul trucks holding liquefied hydrogen created via the liquefaction process.
And in order to facilitate that process, Plug produces two varying-sized liquefaction products for customers seeking to market their hydrogen, a more economical way of carrying the fuel than in its compressed gaseous state, due to its ability to superchill (at -253°C) and condense the gas to liquid. This enables hydrogen marketers to carry more of it per tanker.
Yet, the most efficient way to move hydrogen is via pipelines, only 1,600 miles of which exist today in the U.S. That compares to over 2 million miles of natural gas pipelines, with Plug CEO Andy Marsh calling for “a vastly more expansive [hydrogen pipeline] system” comparable to the gas industry in July 2022 congressional testimony.
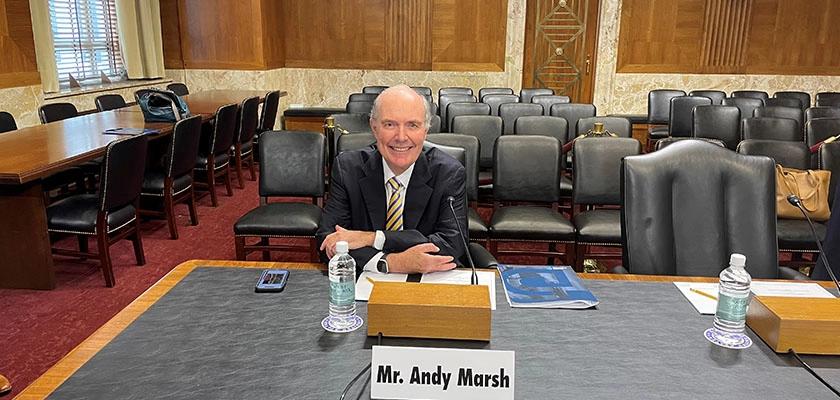
For a more comprehensive review of the broader spectrum of storage and transportation options for moving green hydrogen from upstream electrolyzer to downstream storage point, check out the 2022 article published by Canadian researchers in the International Journal of Hydrogen Energy.
H. Industrial and Commercial Applications of Electrolyzers
One of the major current commercial applications for green hydrogen produced from electrolyzers is fueling stations, which can fuel forklifts, e-mobility, and larger vehicles.
Think of the fuel stations as akin to gas stations dispensing refined diesel or gasoline for vehicles or electric charging stations for battery-powered vehicles. Plug currently stands as a global leader in fueling stations, with customers using them to fuel over 60,000 fuel cell systems used in material handling operations worldwide.
An up and coming application for green hydrogen is Ammonia production. With 70% of all ammonia currently being made from natural gas, and the rest coming from coal, production under the status quo fuels climate change. The EIA has surmised that non-green ammonia is “twice as emissions-intensive as crude steel production and four times that of cement, on a direct CO2 emissions basis.”
But Plug, via its Proton Exchange Membrane (PEM) electrolyzers, can mitigate the greenhouse gas emissions currently embedded in ammonia production and make the vital food-making ammonia fertilizer more sustainable. With stakeholders pushing for industrial actors to green their production processes, Plug’s technology capably aids producers in decarbonizing the chemical compound into green ammonia.
Another application for hydrogen after made from electrolyzers is power-to-gas.
And though still an emerging technology, at least compared to fueling stations which directly dispense hydrogen to customers, power-to-gas applications could be a major part of green hydrogen’s future and a way to make the electricity grid less greenhouse gas-intensive. The process involves injecting hydrogen into the natural gas pipeline as a refined synthetic methane.
I. Maintenance and Safety of Electrolyzers
Maintenance of electrolyzers, as with any industrial equipment, is important for ensuring their optimal functionality and safety.
H2 Tools, an information-sharing database built by the Pacific Northwest National Laboratory of the U.S. Department of Energy, has conveyed that “Proper and timely inspection and maintenance is key to ensuring safe system operation” and that “Reactive maintenance is generally unwise for equipment in hydrogen service.” The Laboratory further recommends a “systematic method” of maintenance which “should be documented and stewarded.”
H2 Tools added that the documentation for maintenance and inspection should “ include a description of any needed follow-up activity and the next scheduled inspection/maintenance activity,” recommending that U.S. Occupational Safety and Health Administration (OSHA) Standard 1910.119 should be the standard utilized for all electrolyzer maintenance.
Beyond maintenance, H2 Tools has also stated that those overseeing electrolyzer operations should utilize a safety culture and that “goals [in that vein] should be clearly communicated and understood by all staff.” The U.S. Occupational Safety and Health Administration also has hydrogen workplace safety regulations on the books, holding companies accountable for the safety of their respective workforces.
J. Advancements in Electrolyzer Technology
Currently, electrolyzers are undergoing great change as they penetrate the market. PEM electrolyzers of the sort Plug uses, for example, are undergoing technological innovation to operate at increasingly higher and more efficient temperature ranges of between 120°C and 200°C.
The U.S. Department of Energy explains that high temperature electrolysis – often just called HTE by industry insiders – “results in very high electrical efficiencies and, hence, potential for low-cost hydrogen production when the steam is produced by either waste heat or a low-cost thermal energy generator.”
Another area of advancement within electrolyzer technology exists in the realm of generating green hydrogen through solar-powered electrolyzers.
In short, this involves utilizing solar technology to generate electricity, which then thereafter powers the electrolyzers producing green hydrogen. Plug’s technology stands ready to carry out that process.
Several such projects exist worldwide, primarily involving solar panel installations placed alongside electrolyzers to ensure maximum efficiency of both energy generation techniques.
K. Future of Electrolyzers
Electrolyzers have the potential to play a key role in the decarbonization efforts of countries and industries around the world. The ability to produce and store hydrogen allows it to be used for a growing number of applications and industrial processes including hydrogen fuel cells, power to gas to power, ammonia and methanol production processes, steel and cement manufacturing among others.
A number of countries have championed hydrogen as a method for meeting their sustainability targets, putting in place policies supporting hydrogen production growth. According to the Green Hydrogen Coalition’s 2nd Edition Green Hydrogen Handbook, as of 2022, Australia, Canada, Chile, the European Union and Japan all have national programs in place. Additionally, the United States’ Inflation Reduction Act includes a robust hydrogen program. India, too, has enacted a National Green Hydrogen Mission.
As countries and companies work together to grow electrolytic hydrogen production, the sky’s the limit on the future of electrolyzers.
L. Economic Considerations of Electrolyzers
One of the biggest barriers to entry for global adoption of electrolyzers, as it stands, is the cost of producing hydrogen from them.
Yet, the cost to produce green hydrogen is project to fall drastically with the passage of the Inflation Reduction Act, which provides producers with a decade of up to $3 per kilogram tax incentives to produce the fuel.
As of 2020, according to U.S. Department of Energy figures, the levelized cost to produce green hydrogen (often called Levelized Cost of Hydrogen, or LCOH) toggled between $4 to $6 per kilogram within PEM electrolyzers. This price point, without the tax incentives, can be achieved “assuming existing technology, low volume electrolyzer capital costs as high as $1,500 [per kilowatt] and grid electricity prices of $0.05 [per kilowatt hour] to $0.07 [per kilowatt hour].”
The cost primarily remains within that range, the DOE concluded, when coupled with both utility scale solar and onshore wind. Others, the DOE pointed out, put production costs at a range of $2.50 to $6.80 per kilogram “from a mix of renewable and grid feedstocks.”
Transportation costs, too, could ultimately drive up the price – speaking to the importance of building out more infrastructure as electrolyzers enable increased green hydrogen production.
The agency’s target range is $2 per kilogram, which means green hydrogen would be produced at a profit once it reaches that level with the new production tax credit in place created by the Inflation Reduction Act. The newly legally sanctioned credits equating to “60% of the average green hydrogen project’s cost,” The Wall Street Journal reported, pointing to financial services industry leader Goldman Sachs’ data.
With the newly codified tax incentives in place, the financial services firm Lazard put the LCOH of green hydrogen from PEM fuel cells at $1.68 to $4.28 per kilogram in an April 2023 report. Plug has a clear development roadmap to green hydrogen at a cost of $1.50 per kilogram.
M. Electrolyzers and Energy Markets
The green hydrogen electrolyzer market will be worth over $120 billion by 2033, a new report by the consultancy IDTechEx has predicted. But to achieve that, many steps will need to be taken in the next decade, experts conclude.
“The industry expects capex to come down as manufacturing capacity increases and capabilities improve through greater levels of automation,” the report notes. “Performance also has a significant impact. For example, the more efficient a system is, the lower the energy consumption…Other key performance metrics for electrolyzer systems include operating lifetime, output pressure and purity, current and power density, start-up times, dynamic range, and minimum load levels.”
The law firm Norton Rose Fulbright, which advises clients on financing hydrogen projects and making them commercial, states that on a project-by-project basis the key to financial success is to “have a bankable offtake scheme.”
The firm points to ammonia as a case in point, an area in which Plug stands ready to supply its green hydrogen to make the product more sustainable. Norton Rose Fulbright also points to speciality vehicles, like forklifts, for which Plug serves as a global leader in providing fuel cells and hydrogen infrastructure.
Lastly, the firm called government support “essential to get the green hydrogen market off the ground,” with that support including “economic incentives and by providing clear and appropriate standards and regulation applicable to the transportation of hydrogen by pipeline, truck and ship.”
N. Environmental Impact of Electrolyzers
From an environmental standpoint, electrolyzers producing green hydrogen can enable significant greenhouse gas reductions, according to a 2022 study published in the journal Sustainable Energy and Fuels.
“Hydrogen powered by offshore wind results in a twentyfold (93–97%) reduction in GHG footprint compared to grey hydrogen and a reduction of 76–94% compared to blue hydrogen,” the study details. “Using solar PV for hydrogen production…equates to a 62–85% reduction compared to grey hydrogen and is in the same range as blue hydrogen (34% increase to 73% reduction in GHG emissions compared to blue hydrogen…).”
Relatedly, a 2019 study published in the journal of Applied Energy concludes that “hydrogen production via proton exchange membrane water electrolysis is a promising technology to reduce CO2 emissions of the hydrogen sector by up to 75%, if the electrolysis system runs exclusively on electricity generated from renewable energy sources.”
O. Performance Metrics of Electrolyzers
While many performance metrics exist for electrolyzers, two are particularly important: efficiency and durability.
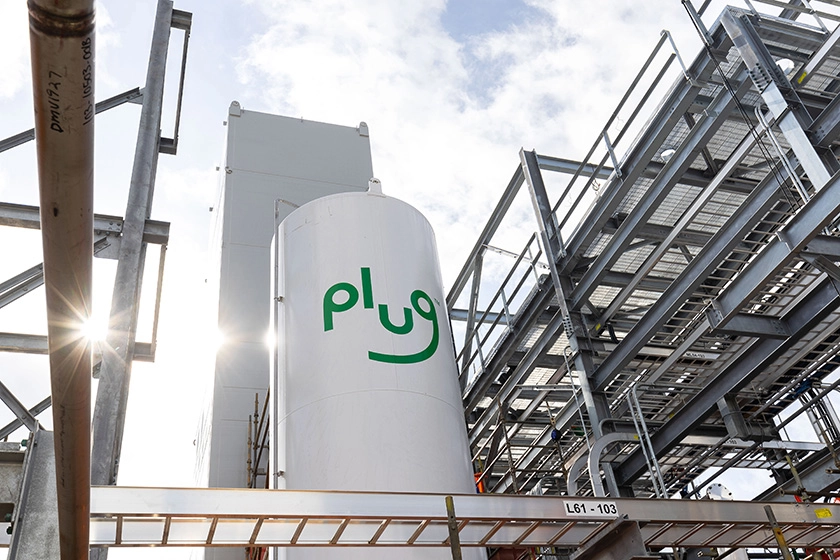
Many factors influence the performance metrics of electrolyzers’ efficiency level, which tallies an average of 61%, according to U.S. Department of Energy statistics.
They include electrolyte quality, electrical resistance of the electrolyte, the type of electrode material used, pressure applied for the current within the electrolyzer, varying types of separator materials, and applied electricity voltage waveform.
A 2017 study also concluded that “The efficiency of water electrolysis at 350°C/100 bars increased about 17%, compared with that at 80°C/1 bar,” meaning higher temperatures have demonstrably made electrolyzers more efficient.
And for durability, Plug’s PEM electrolyzer has a life expectancy of 80,000 hours, a world-leading figure.
P. Quality Control in Electrolyzer Production
Testing procedures in place within the electrolyzer production process ensure quality control in the final product. And Plug has taken a leadership role in quality control mechanisms, participating in the May 2021 International Meeting on Fuel Cell and Electrolyzer Quality Control hosted by the U.S. Department of Energy.
Robust certification standards for green hydrogen also exist, ensuring the product is as green as advertised and marketed, as well as safe.
One of the bodies overseeing safety is the U.S. Department of Energy’s Hydrogen Safety Panel, which maintains the H2 Tools website. In place since 2003, the Panel’s current members include those representing the public and private sectors. The agency has also published a 195-page Hydrogen Equipment Certification Guide, which acts as a domestic companion to the international International Organization for Standardization safety standards for “Hydrogen generators using water electrolysis — Industrial, commercial, and residential applications.”
Similarly, the Switzerland-based Green Hydrogen Organization also maintains a Green Hydrogen Standard seal of authority and certification for hydrogen production to ensure sustainable practices, while the International Renewable Energy Agency has laid out best practices for creating Green Hydrogen Certification.
Q. Regulatory Landscape for Electrolyzers
Electrolyzers are spreading globally, most robustly at the moment in the U.S. and East Asia. That said, 26 countries have either regulatory architecture or policy roadmaps in place to promote hydrogen production, the International Energy Agency’s “Global Hydrogen Review 2022” report has laid out.
In Plug’s home country, the United States, electrolyzers got a major win via the Inflation Reduction Act passed in 2022. The law gave a stamp of approval to the green hydrogen production market by implementing a new Clean Hydrogen Production Tax Credit, a ten-year tax credit (known as 45V) yielding up to $3.00 per kilogram of hydrogen production.
Marsh, of the legislation’s passage, stated that the “passage of the Inflation Reduction Act of 2022 represents our country’s commitment to creating a cleaner future with green hydrogen.”
R. Scaling Up Electrolyzer Technology
While electrolyzer technology is on the rise, manufacturing challenges still do exist to ensure the devices penetrate major regional and global markets. The number one challenge is cost.
A 2020 paper by The Electrochemical Society points to “both the upfront capital expense as well as the operating cost incurred over the product life.” This includes the “high cost of system and cell stack materials, which need to be durable for up to 100,000 [hours]” and “the lack of a robust supply chain for high volume manufacturing to further drive down cost through economies of scale.”
Yet, the paper also notes that PEM electrolyzer technology utilized by Plug is the furthest along and serves as a case study for a “relevant pathway for industrial scale hydrogen generation with tremendous opportunity for continuing cost reduction.”
While capital production costs are one barrier, the other is infrastructure for moving the product to market. As noted above, the biggest current barrier is lack of pipeline infrastructure to efficiently move green hydrogen to market. Increased infrastructure for carrying the product on the roads, too, is needed.
S. Yield Optimization in Electrolyzers
A crucial component to maximize the production value embedded in green hydrogen-producing electrolyzers, over the years, has been to tinker with them to optimize the yield of green hydrogen produced.
One study pointed out that the “efficiency of the PV-electrolysis system was optimized by matching the voltage and maximum power output of the photovoltaics to the operating voltage of proton exchange membrane (PEM) electrolyzers,” continuing, “The optimization process increased the hydrogen generation efficiency to 12% for a solar powered PV-PEM electrolyzer that could supply enough hydrogen to operate a fuel cell vehicle.”
Another way of tinkering is through the materials that become electrolyzer components.
The National Renewable Energy Laboratory is currently performing research on higher performance catalysts and “new materials for water splitting.” Two large-scale research projects remain ongoing in that vein within the Laboratory: the Liquid Sunlight Alliance Hub and the HydroGEN Advanced Water-Splitting Materials Consortium.
But it’s catalyst materials that have been of particular interest for those studying optimization of green hydrogen electrolyzers.
“The number of catalyst materials studied for green hydrogen production has increased over the past decade, while the number of materials studied for use in hydrogen storage and fuel cell production has fallen, consistent with their relative levels of technical maturity,” a 2022 study published by the American Chemical Society details.
T. Zero-Emission Hydrogen Production with Electrolyzers
Green hydrogen made from electrolyzers could be a game-changer for climate change as the market for it flourishes globally. But with every great opportunity also comes challenges.
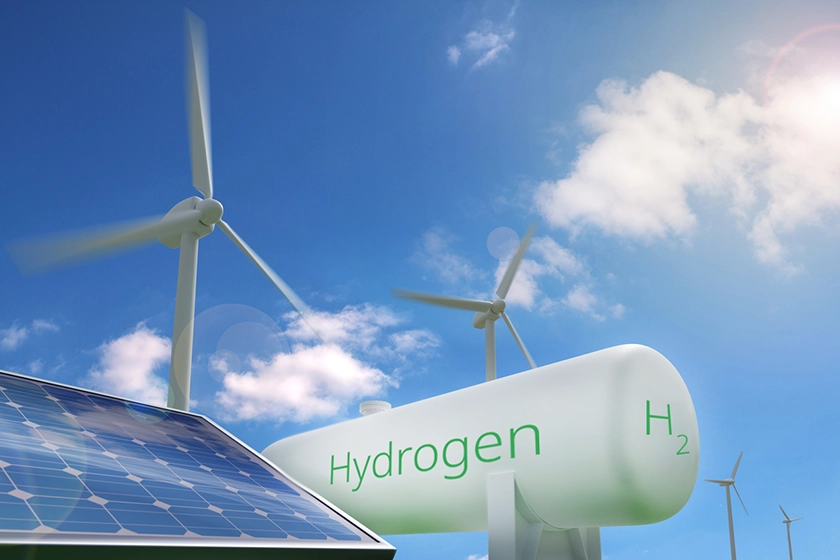
While the opportunity is bountiful, the challenge of truly hitting the jackpot comes down to the age-old infrastructure question.
“For green hydrogen to achieve commercialization as a carbon-free fuel, the industry must overcome the classic chicken-and-egg dilemma: putting in place the needed infrastructure – including hydrogen transport, hydrogen vehicle refueling stations, and end users equipped to use hydrogen – before hydrogen production is fully scaled,” Leidos, a defense contracting and information services company, explained in a 2021 blog post. “There is less incentive to construct the supporting infrastructure and deploy end-user technologies if the hydrogen production facilities are not available and vice versa.”
Other challenges include finding suitable places for placing electrolyzers, energy loss throughout the value chain, as well as water costs.
U. Techno-Economic Analysis of Electrolyzers
According to techno-economic analyses, which measure and evaluate forward-looking economic performances of assessed technologies, can achieve parity with fossil fuel-based hydrogen between 2025 and 2040.
And in comparing electrolyzer types to one another, the Fraunhofer Institute for Solar Energy Systems ISE has concluded that the total cost of ownership of a PEM electrolyzer totals one-third that of alkaline electrolyzer.
V. Utility-Scale Electrolyzers
For green hydrogen electrolyzers to achieve material scale, integration with the existing renewable energy utilities grid will be of utmost importance.
The Climate Council — funded by financial services companies such as Blackstone, Blackrock, Capital One, and J.P. Morgan, as well as the World Bank Group — opines that “Expanding renewable generation capacity to first and foremost deliver electricity to grids should be the priority for where wind or solar power are directed.”
Fortunately, doing so is feasible, according to a 2022 review article covering the integration of green hydrogen electrolyzers with solar and wind projects published by the journal Environmental Science and Pollution Research.
The article concluded that “authorities must enhance their energy budget to encourage green hydrogen” and that “increasing production would need developing hydrogen infrastructure, a massive effort that requires a solid plan and political backing.”
“Therefore, the authorities should collaborate with recognized firms in creating green hydrogen infrastructure to develop a strategic plan for green hydrogen’s success in the market and the expansion of such infrastructure,” the study concludes.
As explained above in “H,” power-to-gas applications can also serve as a means of linking green hydrogen to the electricity grid on the back end. Excess heat generated from the electrolysis process can be fed onto it as a zero-carbon fuel source.
Power Magazine reported that, as of 2019, “About 143 power-to-gas projects producing hydrogen and/or methane have operated since 1988 in 22 countries.” A list of all existing power-to-gas projects as of September 2019 can be seen here.
W. Value Chain of Electrolyzers
Electrolyzers do not come about by magic, despite their mystique. Instead, they require a bevy of resources to come to fruition.
- Raw Materials: The production of electrolyzers requires raw materials such as metals (e.g., platinum, nickel), polymer membranes, catalysts, and other specialized materials.
- Components: Various components are needed for electrolyzer assembly, including electrodes (anode and cathode), proton exchange membranes (PEM), bipolar plates, gas diffusion layers, current collectors, and electrical connections.
- Human capital: Used in the manufacturing process, for quality control, shipping, installation, operation and maintenance.
- Distribution: Hydrogen can be transported via various means, such as pipelines, cryogenic tanker trucks, or shipping containers, to reach end-users.
X. Water Management in Electrolyzers
Management of water, as in the production of anything in an era of increasing water scarcity, is top of mind in utilizing electrolyzers. In that vein, Plug’s PEM electrolyzers make use of Industrial water.
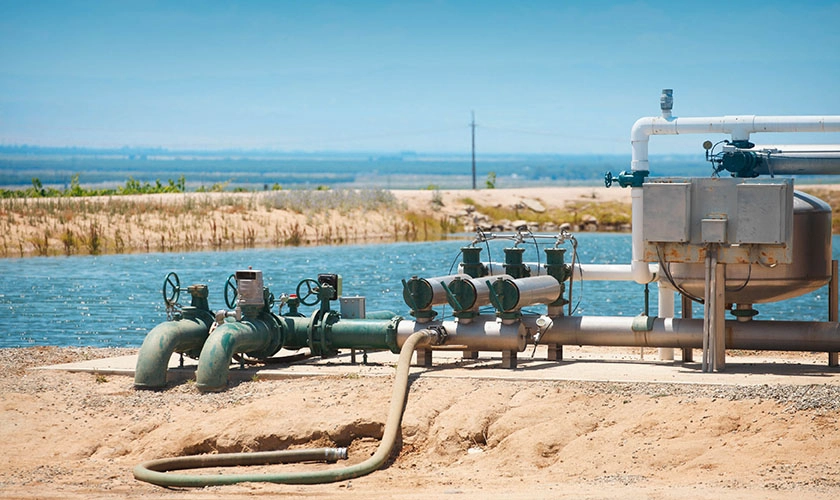
It differs from drinking water, used in industries such as smelting facilities, petroleum refineries, as well as the food, paper, and chemical industries. Plug utilizes a water filtration process to remove calcium, magnesium, and other mineral deposits that would poison the electrolysis process.
Over 910,000 liters of water are used to manufacture 75,000 kilograms of hydrogen per day. This equates to the water used on a large dairy farm, though is less than used to grow alfalfa or almonds en masse.
Importantly and most notably, the green hydrogen electrolysis process uses less water than all major electricity production methods besides geothermal.
Y. Plug’s Role in the Electrolyzer Industry
Plug has built out its electrolyzer production capacity to meet a historical moment for green hydrogen demand, as countries and businesses make a generational shift to renewable energy in accordance with midcentury “net zero” emissions climate goals.
Among other things, Plug stands ready to clean up currently greenhouse gas-emitting industries, such as ammonia and methanol.
Plug produces three different electrolyzer products, while it can also produce built-to-order and custom-engineered products, produced in facilities located both in the U.S. and Europe.
In 2022 alone, Plug’s electrolyzers have helped both Canadian and Hungarian oil companies clean up their refinery operations, teamed up with Danish and French hydrogen companies to construct both countries’ largest ever green hydrogen electrolyzer facilities, and signed a 120-megawatt electrolyzer deal to produce green hydrogen along the Gulf Coast. The 1 GW deal with the Denmark-based company H2 Energy Europe is the largest ever signed in history.
In March 2023, Plug also signed a deal with a Netherlands-based energy company to book 100 MW of green hydrogen electrolyzers to power its facilities located at the Port of Rotterdam.
By mid-decade, Plug aims to produce 500 tons per day of green hydrogen at facilities across the U.S. and globally across five continents.
For a more extensive look under the hood at a Plug electrolyzer production facility and what can be achieved within, check out the video below. And to learn more about how our team can help you produce green hydrogen to fuel your needs, please touch base with our electrolyzer team.
Z. Conclusion
Electrolyzers are the bread-and-butter for the growth of green hydrogen and a more sustainable energy future, particularly in tough to decarbonize sectors.
And the future looks bright for the technology. Bloomberg has reported that the outlook looks bright for electrolyzers, comparing it to the “hockey stick”-like growth seen in the past decade for solar energy’s ascent.
“Measured by the amount of power the machines consume, worldwide electrolyzer sales doubled from 200 megawatts in 2020 to 458 in 2021,” the publication reported in 2022. “They’re expected to triple this year, reaching anywhere from 1,839 megawatts to 2,464 megawatts.”
The International Energy Agency has reiterated the hockey stick thesis, hypothesizing that after reaching a global electrolyzer capacity of 8 GW per year in 2022, that could spike to 134 to 240 GW by 2030.
BloombergNEF has estimated even higher at 242 GW, noting that it believes Plug will sit among a select few companies “leading the manufacturing” of electrolyzers during that period. “Cumulatively, around $130 billion will be spent on electrolyzers between now and 2030,” the research company explained, calling what lay ahead for green hydrogen “breakneck growth.”
Plug, with its PEM electrolyzer stack technology, stands ready to champion green hydrogen and work with partners current and prospective to equip them with electrolyzers to produce the fuel.
To discuss your electrolyzer project, contact us here.