Australian firm says it can slash the cost of green hydrogen-based iron for steelmaking, but do its claims stack up?
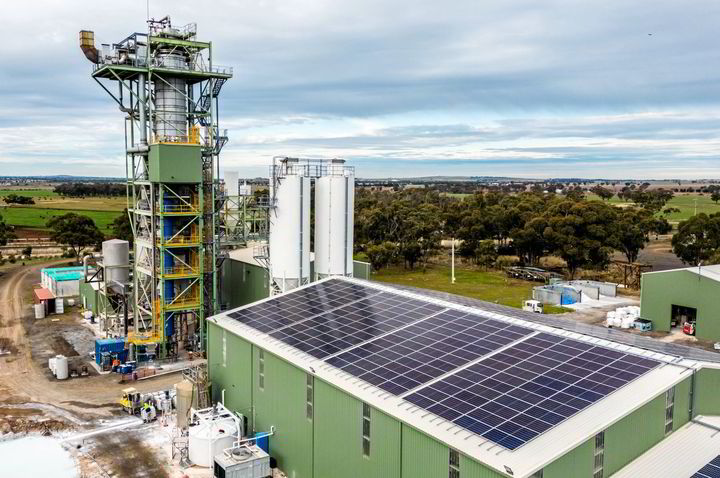
An Australian green tech company says it can bring down the cost of renewable hydrogen-based direct-reduced iron (DRI) for use in steelmaking, by reducing the amount of H2 used as a chemical reductant.
It also claims that by reducing hydrogen consumption, it can produce H2 DRI at costs competitive with those of fossil-fuel-based iron — but do either of these claims stack up?
New South Wales-based Calix, which specialises in technology for use in mineral and chemical processing, found that it could produce a processed form of DRI called hot briquetted iron (HBI), for around A$630-800 per tonne (US$411-522), using a 15MW electrolyser.
The company gave its cost estimates as part of a front-end design and engineering (FEED) study it has been carrying out for a proposed demonstration of its Zero Emissions Steel Technology (which it calls Zesty) at an as-yet unnamed site in Australia.
The study assumed a levelised cost of hydrogen of US$3.55-4/kg (based on the upfront cost of electrolysers and electricity priced at US$23-31/MWh, which it calculated using forecast spot pricing and transmission and connection costs) and iron ore at US$35/tonne.
The main cost savings would be achieved by reducing the amount of expensive hydrogen used in the process, Calix said.
Article continues below the advert
The Zesty process achieves this by pre-heating the H2 before it adds it to a calciner (a tall cylinder used for processing chemicals and minerals), where it chemically strips the oxygen from iron ore to produce direct-reduced iron that can then be processed into HBI for onward sale (and eventually made into steel).
The process leaves some excess hydrogen that can then be re-used, and the exhaust steam (H2O formed by the hydrogen and stripped oxygen) is either fed back into the electrolyser for further hydrogen production, or fed into an on-site steam-powered power generator, which in turn can help power the electrolyser (along with renewable electricity), essentially recycling the process heat in a closed loop.
Calix claims that using fewer kilograms of expensive hydrogen gives it a cost advantage over other H2-based DRI processes.
The company told Hydrogen Insight that it would need 54kg of H2 to make each tonne of HBI — the bare minimum needed to chemically reduce the iron ore — with unreacted volumes left over then recycled back into the process.
For this, Calix estimates it will need to produce or buy in 1,500 tonnes of green hydrogen per year for its 30,000 tonnes-per-annum demonstration HBI plant (which actually suggests 50kg of H2 per tonne of iron).
In theory, this claim does appear robust. Thyssenkrupp’s tkH2Steel DRI project at the company’s plant in Duisburg, Germany, could need to use an extra 4kg of hydrogen per tonne of iron, according to Hydrogen Insight‘s calculations. Thyssenkrupp’s estimates that it would use 400 tonnes of H2 per day (146,000 tonnes a year) to make 2.5 million tonnes of DRI annually. This suggests it would need 58.4kg per tonne of DRI.
So, if hydrogen costs were approximately $3.55-4/kg (as modelled in Calix’s study), this should mean that each tonne of DRI would carry $15.62-17.60 less in H2 costs than Thyssenkrupp’s — or up to $44m a year at the latter’s Duisburg plant.
“Zesty’s cost estimates are for a 30ktpa, first-of-its-kind demonstration plant,” said Mike Walsh, Calix’s manager for corporate affairs. “Further cost savings are expected through economies of scale for larger commercial plants.”
Calix also claims that it can produce DRI at costs similar to those of fossil fuel-based equivalents, without taking subsidies into account.
However, there are questions about how fair the comparison is with different steel production routes, as Calix appears to have compared the cost of making its HBI with the compound costs of making both iron and steel together.
It compares its estimated $411-522/tonne HBI costs with fossil-fuel equivalents, citing International Energy Agency (IEA) figures which suggest traditional steel production costs of $300-475/tonne. However, the IEA figures relate to the cost of making pure iron from iron ore in a coke-fired blast furnace (BF) and then turning it into steel in a basic oxygen furnace (BOF), not just the cost of producing iron.
Calix told Hydrogen Insight that it used the IEA figures because they are credible and easily accessible, noting that some of the data it used to make its claim is proprietary and unavailable to the general public.
The costs of using its HBI in either a blast furnace or an electric arc furnace to create low-emissions steel — so that a like-for-like comparison could be made using the IEA figures — was beyond the scope of the Zesty FEED study, Walsh said.
Nevertheless, the HBI produced by the Zesty process has a purity of around 75-92%, making it ideal for use in facilities that are still using the BF-BOF route, which can accept lower grade metallic iron than facilities using electric arc furnaces, which need iron purities in excess of 95%, depending on the temperature of the smelter.
The BF-BOF route typically used by the vast majority of steelmakers is incredibly carbon-intensive — accounting for 7-8% of global emissions — so the industry is now looking at the use of hydrogen-based DRI instead.
In this case, Calix’s HBI could reduce the emissions of steel made with a coke-fired basic oxygen furnace by up to 80%, the company said.
When used with a renewables-powered electric arc furnace, emissions would be reduced by up to 100%.
The US$1.3m FEED and pre-FEED studies for the demonstration project, which build on a pilot scheme of the Zesty technology at Calix’s existing cement and lime project in Victoria, Australia, was carried out with US$617,000 in support from Australia’s federal government, ahead of a final investment decision.
Total capex costs for the demonstration project are under wraps while Calix negotiates financing deals, the company said